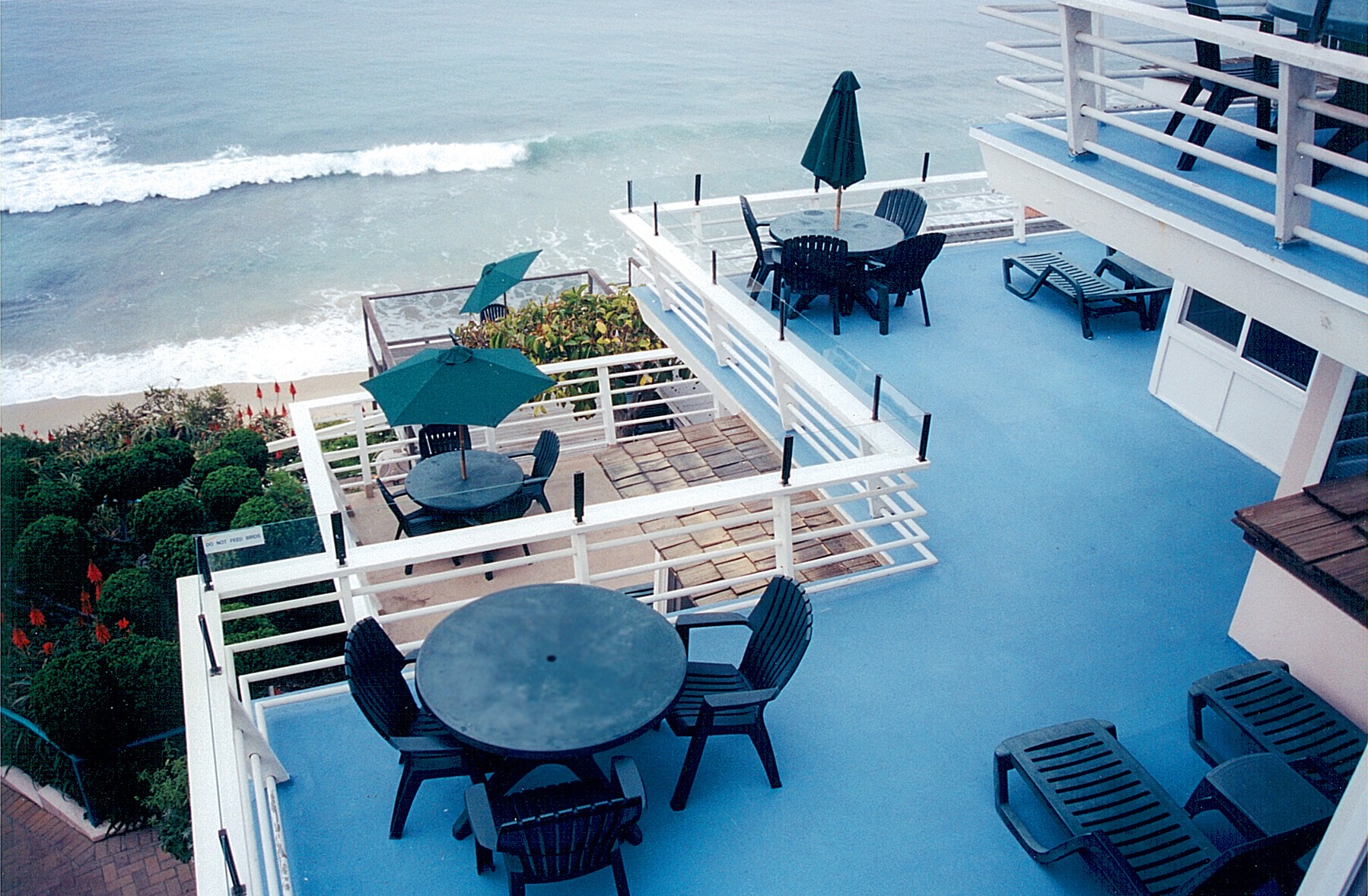
SECTION 07100
ALL DECK Fire Retardant Waterproof Non-Skid Deck Coating System
PART 1 – GENERAL
1.01 SECTION INCLUDES
A. ALL DECK fluid applied, fiberglass reinforced, fire retardant, decorative, non-skid, textured, waterproof acrylic deck coating system.
B. Perimeter edging and flashing.
1.02 RELATED REFERENCES
A. Section 09980: Concrete substrate with medium broom finish.
B. Section 07180: Traffic CoatingsC. Section 07900: Joint Sealers
1.03 REFERENCES
A. ASTM D903 – Peel or Stripping Strength of Adhesive Bonds.
B. ASTM D2523 – Testing Load-Strain Properties of Roofing Membranes.
C. ASTM D3393 – Coated Fabrics – Waterproofness.
D. ASTM E84 – Surface Burning Characteristics of Building Materials.
E. ASTM E96 – Water Vapor Transmission of Materials.
F. ASTM E108 – Standard Method of Fire Test of Roof Coverings.
G. NFPA – National Fire Protection Association.
H. UBC – Uniform Building Code – 32.7.
I. U/L – Underwriters Laboratories – 790.
J. EPA – Environmental Protection Agency – V.O.C. Ruling
K. CSFM – California State Fire Marshal Listing
L. L.A. – City of Los Angeles Research Report
1.04 PERFORMANCE REQUIREMENTS
A. Install ALL DECK coating to conform to the following:Property ASTM Test ResultMoisture Vapor Permeability E96 0.18-0.22 permsPeel Strength D903
Plywood 11-18 psi
Concrete 3.3-7.6 psiFire Rating E108
Non-Combustible Surface Class A
Combustible Surface Class
B1.05 QUALIFICATIONS
A. Applicator: Company specializing in resinous matrix coating applications with documented experience.
B. Supervisor: Trained by product manufacturer.
1.06 MOCK-UP
A. Provide mock-up of 10 square feet of coating and 3 lineal feet of base under provisions of Section 01400.
B. Provide analysis of mock-up under provisions of Section 01400.
C. When accepted, mock-up will demonstrate minimum standard for the work. Mock-up may not remain as part of the work.
1.07 SUBMITTALS
A. Submit product data under provisions of Section 01340.
B. Submit two samples 12 x 12 inches in size illustrating color and variation.
C. Submit ALL DECK manufacturer’s installation instructions under provisions of Section 01340.
D. Material Safety Data Sheets for each layer of coating system.
E. Physical Properties analysis for each layer of coating system.
1.08 OPERATIONS AND MAINTENANCE DATA
A. Submit cleaning and maintenance data under provisions of Section 01700.
B. Include procedures for stain removal, repairing surface, and cleaning.
1.09 DELIVERY, STORAGE, AND HANDLING
A. Deliver materials in original packages and containers with seals unbroken and bearing manufacturer’s labels containing ALL DECK brand name and directions for storage and mixing with other components.
B. Store materials to comply with ALL DECK manufacturer’s directions to prevent deterioration from moisture, heat, cold, direct sunlight, or other causes. Material shelf life approximately 5 years except mixed ALL DECK Textured Base Coat. Mixed ALL DECK Textured Base Coat shelf life approximately 6 months.
C. Keep materials from freezing.
1.10 ENVIRONMENTAL REQUIREMENTSA. Comply with ALL DECK Coating manufacturer’s directions for maintenance of substrate temperatures, ventilation, and other conditions required to execute and protect work.
1.11 WARRANTY
A. Manufacturer’s Warranty: Ten (10) year limited material warranty only. Issued in writing by manufacturer at conculsion of project.
PART 2 – PRODUCTS
2.01 MANUFACTURER
A. Provide ALL DECK COATING SYSTEM materials and products as manufactured by:
FSC Coatings
5360 Eastgate Mall, San Diego, CA 92121
Toll Free: (800) ALL-DECK (255-3325)
E-mail: info@alldeck.com
2.02 MATERIALS
A. ALL DECK Acrylic Patching Compound: Use for filling small to medium sized cracks and depressions and over seam metal.
B. Seam Metal: Light gauge, hot zinc dipped, sheet metal for finishing wood joints in substrate.
C. Fiberglass Mat: Use for reinforcing first coat.
D. Fiberglass Mesh: Use for reinforcing flexible joint system.
E. ALL DECK Clear Acrylic Sealer: Use to prepare concrete and aggregate concrete substrates. Use over plywood when Fire Rated installation required.
F. ALL DECK Acrylic Caulking Compound: Use to apply fiberglass mesh for flexible joint system. To fill joint in concrete surfaces.
G. ALL DECK Laminating Resin: Acrylic resin used to laminate fiberglass mat to prepared substrate.
H. ALL DECK Textured Basecoat Kit: Acrylic resin and aggregate compound which, when mixed, can be applied by roller, brush, trowel or texture gun.
I. ALL DECK Finish Resin: Final waterproof acrylic coating application.
J. Optional ALL DECK Confetti Finish: Sprinkled or sprayed dry acrylic confetti particles by hand or hopper gun onto wet Finish Resin for decorative effect.
K. Optional ALL DECK Confetti Finish: Sprinkle or sprayed dry acrylic confetti particles by hand or hopper gun onto wet Finish Resin for decorative effect.
2.03 COLORS
A. Provide coating in manufacturer’s standard color pallet.
B. (Provide custom colors.)
C. (Provide contrasting Confetti colors.)
2.04 MIXINGA. Mix coating components in accordance with manufacturer’s printed instructions.
PART 3 – EXECUTION
3.01 EXAMINATION
A. Verify that substrates are ready to receive work, that substrate surface is clean, dry and free of substances which could affect bond.
B. Do not begin work until concrete substrate has cured. Wood substrate should be dried to a maximum content of 12 percent.
C. Beginning of installation means acceptance of existing substrate.
3.02 SUBSTRATE PREPARATION
A. Perform preparation and cleaning procedures in compliance with flooring manufacturer’s instructions for particular substrate conditions involved and as herein specified.
B. Clean substrate surface free of foreign matter; seal with All Deck Clear Acrylic Sealer where required.
C. Substrate
1. Concrete: Grind off all irregularities. Fill all hairline cracks with Patching Compound. Apply fiberglass mesh and Acrylic Caulking Compound, followed by fiberglass mat and Laminating Resin to all moving cracks, as per manufacturer’s instructions.
2. Plywood: Prepare wood joints with seam metal. Install flashing and counter flashing as per plans. Apply two thin coats of Patching Compound to all metal, to cover nails, and to feather out, in accordance with manufacturer’s instructions.
3.03 COATING APPLICATION
A. Apply in accordance with manufacturer’s printed instructions.
B. First coat shall consist of fiberglass mat laminated to the prepared substrate with Laminating Resin at the rate of approximately 40-60 square feet per gallon. Follow manufacturer’s instructions for splicing mat and perimeter detailing.
C. If there is a substantial time lapse between the first and second coat of application, or the second and third coat of application, clean surface free of foreign matter in compliance with flooring manufacturer’s instructions.
D. Second coat is Textured Basecoat Kit consisting of Textured Basecoat Resin mixed with Basecoat Aggregate compound. This coat can be applied by brush, roller, trowel or hopper-type texture gun. Follow manufacturer’s instructions for application by the various methods. Cut in coves and edges with Textured Basecoat. Apply Textured Basecoat to balance of area, at a coverage rate of approximately 100 square feet per one gallon kit, spray or roll formula.
E. Final coat is Finish Resin applied at the approximate rate of 125 square feet per gallon.
F. Repair bubbles and wrinkles in accordance with manufacturer’s instructions for specific type of situation.
G. Optional Confetti Finish applied at the approximate rate of 100 square feet per pound.
H. Optional Confetti Finish applied at the approximate rate of 400 square feet per 4 pound bag. Color selection and number of colors up to customer. Colors are mixed together and broadcast onto wet Finish Resin using dry hopper gun, splatter gun, lawn seeder, or hand.
3.04 PROTECTION
A. Protect deck coating materials from damage and wear during construction operation. Where temporary covering is required, comply with manufacturer’s recommendations for protective materials and method of application. Remove temporary covering prior to cleaning for final inspection.
B. Protect elements surrounding the work of this Section from damage of disfigurement.C. Restrict traffic from application area until coating is dry; minimize traffic on coating for the approximate two week curing period.
Need further assistance? Don’t hesitate to contact us for personalized advice. We’re here to help.